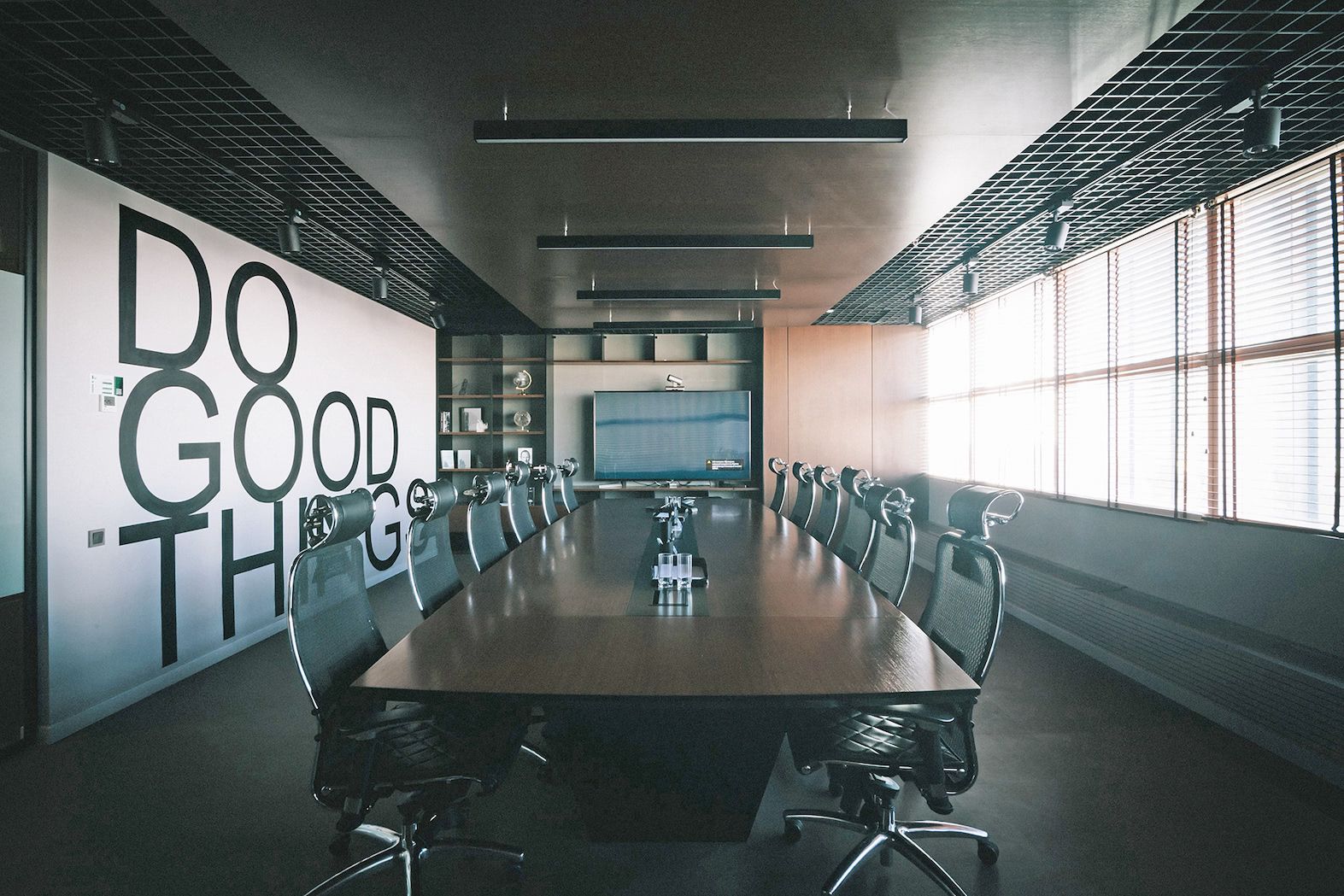
L'importanza del training per il successo dell'azienda
Il training degli operatori è la via obbligata per il successo di ogni organizzazione. Perchè?
Per molte ragioni...
“Education is to teach people what they don’t know. Training is to support people to get tangible results through persistent practice to internalize what they already know. Education without training is meaningless.” – Taiichi Ohno
Prendo a prestito questa frase pubblicata da un amico in un suo post per ribadire un concetto che mi è molto caro: il training degli operatori è la via obbligata per il successo di ogni organizzazione. Perchè? Per molte ragioni:
- innanzitutto per questioni di capacità di effettuare il lavoro: senza un adeguato training gli operatori non sanno svolgere il lavoro che è stato loro assegnato (e magari anche spiegato o dimostrato minuziosamente….ma appunto solo spiegato o dimostrato, senza pratica), o lo sanno svolgere solo parzialmente o in modo diverso da quello richiesto, con evidente impatto sul risultato finale;
- poi per questioni di qualità. Se non viene effettuato un training adeguato e sufficiente a mettere l’operatore nelle condizioni di eseguire sempre il lavoro con la stessa qualità, è inevitabile avere pezzi (o esecuzioni) differenti tra loro, alcuni buoni, altri difettosi. Di conseguenza si renderanno necessarie riprese e rilavorazioni, con gli evidenti impatti sul fronte del costo finale del prodotto (o del servizio);
- e ancora, per questioni di rispetto dei tempi di esecuzione del lavoro. Grazie ad un adeguato training non solo si può insegnare ad un operatore a svolgere in modo corretto un dato lavoro, ma anche ad eseguirlo nel tempo assegnato. Questo ha importanti implicazioni su almeno due fronti: quello del rispetto dei costi di produzione – se so che per assemblare un dato prodotto i miei operatori impiegano stabilmente 15 minuti, posso calcolare con certezza il costo diretto della manodopera su quel prodotto. Se poi sono anche ragionevolmente certo che la qualità del lavoro dei miei operatori non crea scarti o rilavorazioni, non avrò extra costi derivanti da tali tipi di problemi. Aggiungendo tutti gli altri costi diretti e indiretti che gravano sul mio prodotto singolo (di cui tralascio la descrizione dettagliata) alla fine, grazie ad un processo di produzione stabile, sarà possibile calcolare con precisione il costo finale di produzione, e di conseguenza definire il prezzo che permetta di ottenere anche un certo guadagno. L’altro fronte è quello del rispetto dei tempi di consegna. Se il tempo di esecuzione è stabile e conosciuto, e non ci sono problemi di approvvigionamenti o di malfunzionamenti delle macchine, saremo in grado di programmare con certezza la produzione in modo da rispettare i tempi di consegna pattuiti con il cliente;
- poi per ragioni di sicurezza sul lavoro: un adeguato training insegnerà agli operatori come svolgere una data operazione in modo sicuro, oltre che corretto. Si potranno evitare così incidenti o, peggio ancora, ferimenti degli operatori, con tutte le conseguenze che questi comportano non solo dal punto di vista economico, ma anche umano e giuridico;
- infine per ragioni di miglioramento dei processi. Per argomentare questa mia affermazione ancora una volta prendo a prestito una frase di Taiichi Ohno, il padre del Toyota Production System: ” Without standards, there can be no kaizen.” Per poter avviare E SOSTENERE con successo il miglioramento di un dato processo, è fondamentale che tale processo sia standardizzato e stabile, altrimenti il miglioramento non attecchisce e soprattutto non dura nel tempo. E come si fa a standardizzare e stabilizzare un processo? Attraverso il training agli operatori. Se a tutti gli operatori viene insegnato ad eseguire un dato lavoro nello stesso modo, tutti impareranno a farlo in quel dato modo e nel tempo assegnato, rendendolo così standardizzato e stabile (senza variazioni). E se tutti lo svolgono allo stesso modo, quando quel modo viene migliorato (e viene fatto il training), il miglioramento vale per tutti. In questo modo si rendono stabili non solo i processi, ma anche i miglioramenti che vengono introdotti in quei processi.
Ci sono molti modi di fare training, ma molto spesso non sono sicuri e affidabili.
C’è un metodo sicuro ed affidabile che funziona sempre, se viene applicato. Questo metodo fu sviluppato negli USA durante la Seconda Guerra Mondiale e fu usato in modo intensivo negli stabilimenti e nelle imprese americane. Il metodo si chiama TWI: Training Within Industry e alla fine della Guerra Mondiale fu esportato in Europa e in Giappone dove ebbe, ed oggi ancora ha, un enorme successo. La Toyota fu una delle aziende che lo adottò negli anni ’50, lo stesso Taiichi Ohno era un Trainer per Job Instruction, proprio per introdurre e stabilizzare gli standard, e ancora oggi ne fa un uso quotidiano per favorire la crescita dei propri supervisori.
Ai nostri giorni il TWI sta tornando prepotentemente alla ribalta, ed è utilizzato diffusamente nel mondo da organizzazioni sia di grandi e grandissime dimensioni, che da quelle di taglia più piccola che hanno capito quanto importante sia disporre di standard efficaci, e di una forza lavoro addestrata ad applicarli quotidianamente.
Cerchiamo allora di considerare il training non più come un costo, ma come la via necessaria per raggiungere il successo della nostra impresa!
English version
“Education is to teach people what they don’t know. Training is to support people to get tangible results through persistent practice to internalize what they already know. Education without training is meaningless.” – Taiichi Ohno
I use this phrase above, published by a friend in another post, to stress a concept that is very important to me: “training of operators is the only way to go for the success of any organization. Why? For many reasons:
– first of all for a matter of ability to carry out the work: without adequate training the operators do not know how to carry out the assigned work(and perhaps even explained or shown in detail … unfortunately only “explained” or “shown”), or they know how to perform it only partially or in a different way, with an obvious impact on the final result;
– then for quality issues. If adequate and sufficient training is not given to enable the operator to always perform the work with the same quality, it is inevitable to have different pieces (or executions), some good, others defective. Consequently, it will be necessary to rework, with the obvious impact on the final cost of the product (or service).
– and again, for a matter of respect of cycle time. Thanks to adequate training, not only can an operator be taught to perform a given job correctly, but also to perform it in the allotted time. This has important implications on at least two fronts: the one of respecting production costs – for instance, if I know that it takes my operators 15 minutes to assemble a given product, I can calculate with certainty the direct cost of labor on that product. And if I am also reasonably certain that the quality of the work of my operators does not create waste or rework, I will not have extra costs deriving from these types of problems. By adding all the other direct and indirect costs that affect my single product (no need to detail them here) at the end, thanks to a stable production process, it will be possible to accurately calculate the final cost of production, and consequently define the price which also allows you to obtain a certain profit. The other front is the one related to respect of delivery time. If the execution time is stable and known, and there are no problems with materials supplies or machine stops, we will be able to plan production with certainty in order to respect the delivery times required by customers.
– then for safety reasons: adequate training will teach operators how to carry out a given operation in a safe and correct way. In this way, accidents or worse, injuries to operators, can be avoided with all the benefits not only from an economic point of view, but also from a human and legal point of view;
– finally for process improvement reasons. To explain this statement, I once again will use a quote from Taiichi Ohno, the father of the Toyota Production System: “Without standards, there can be no kaizen.” In order to successfully initiate AND SUPPORT the improvement of a process, it is essential to standardize and stabilize it, otherwise the improvement won’t be installed and, above all, it won’t last over time. And how do you standardize and stabilize a process? Through operators training. If all operators are taught to perform a given job in the same way, they all will learn to do it in the given way and in the allotted time, thus making it standardized and stable (without variations). And if everyone does it the same way, when that way is improved (and training is done), the improvement applies to everyone. In this way, we will stabilize not only the processes , but also the improvements brought to those processes.
There are many ways to train operators, but very often they are not sure and reliable.
There is a sure and reliable method that always works, if it is applied. This method was developed in the US during World War II and was used extensively in American companies. The method is called TWI: Training Within Industry and at the end of the World War it was exported to Europe and Japan where it had, and still has, enormous success. Toyota was one of the companies that adopted it in the 1950s (Taiichi Ohno himself was a Job Instruction Trainer) to introduce and stabilize the standards, and still today is using it day in – day out to support the growth of its supervisors.
Nowadays, TWI is making a strong comeback, and is widely used around the world by both large and very large organizations, as well as by smaller ones who have understood how important it is to have good standards, and a well trained workforce able to apply them in their daily work.
So let’s stop to consider training as a cost, and see it as the necessary way to achieve success in our business!